Getting Welding Quality: Unveiling the Tricks of WPS Implementation and Optimization
In the world of welding, achieving excellence is a quest that rests on the meticulous implementation and optimization of Welding Procedure Specifications (WPS) These foundational files function as the backbone of welding procedures, dictating the parameters and treatments needed for creating high-quality welds constantly. However, the secrets to opening the full potential of WPS exist not only in comprehending its importance yet also in understanding the complexities of its execution and optimization. By delving right into the crucial elements, techniques, difficulties, and finest methods connected with WPS, a globe of welding quality awaits those that are ready to discover its midsts.
Value of WPS in Welding
The Value of Welding Procedure Specifications (WPS) in the welding industry can not be overemphasized, acting as the foundation for making certain consistency, high quality, and safety and security in welding procedures. A WPS offers comprehensive directions on exactly how welding is to be performed, consisting of crucial variables such as products, welding processes, joint style, filler metals, preheat and interpass temperatures, welding currents, voltages, travel rates, and extra. By sticking to a distinct WPS, welders can keep uniformity in their job, leading to constant weld top quality across various jobs.
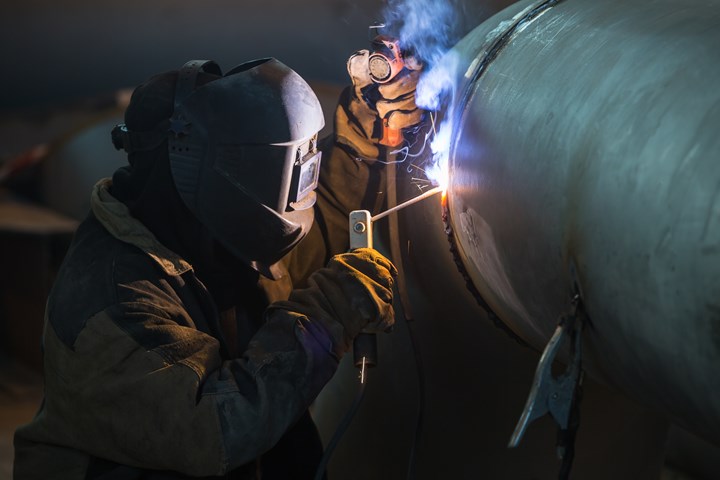
Key Components of WPS
Reviewing the essential parts of a welding procedure requirements (WPS) is vital for recognizing its role in welding procedures. An extensive WPS consists of a number of key components that assist welders in accomplishing high quality and uniformity in their job. One crucial aspect of a WPS is the welding process specification, which describes the specific welding processes to be made use of, such as gas tungsten arc welding (GTAW) or secured metal arc welding (SMAW) Additionally, the WPS includes details on the welding products, such as the kind and requirements of the base steel and filler steel to be utilized. The WPS likewise defines crucial variables like welding criteria, interpass and preheat temperature needs, and post-weld heat treatment procedures. Additionally, it includes information on joint design, fit-up, and any unique techniques or safety measures required for the welding operation. By integrating these crucial elements right into the WPS, welding procedures can be standard, guaranteeing high quality, performance, and safety in welding operations.
Techniques for WPS Optimization
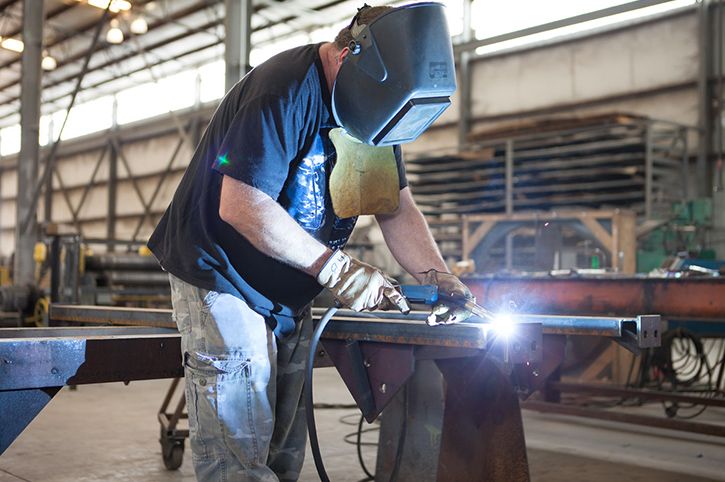
Second of all, training and qualification of welding personnel according to the details needs of the WPS is critical. Giving extensive training programs and guaranteeing that welders are accredited to carry out treatments described in the WPS can result in better welds and minimized rework.
Additionally, leveraging innovation such as welding software and monitoring systems can help in optimizing WPS. These devices can help in tracking variables, making sure criteria are within defined limitations, and supplying real-time responses to welders, allowing them to make instant changes for boosted weld top quality.
Common Challenges and Solutions
Dealing with challenges in implementing the methods for WPS optimization can hinder welding procedures' performance and quality. One common obstacle is inadequate training or understanding of the welding procedure specifications (WPS) among the welding team.
An additional obstacle is the absence of proper documentation and record-keeping, which is necessary for WPS optimization. Without clear documents of welding parameters, products made use of, and evaluation results, it comes to be challenging to identify locations for enhancement and ensure uniformity in welding procedures. Carrying out a durable documentation system, such as electronic welding management software program, can aid simplify record-keeping and promote information evaluation for continual renovation.
Additionally, irregular welding tools calibration and maintenance can position a considerable difficulty to WPS optimization. Normal tools checks, calibration, and upkeep routines must be stuck to strictly to make sure that welding criteria are precisely managed and preserved within the defined tolerances (welding WPS). By addressing these typical difficulties with proactive remedies, welding operations can boost efficiency, quality, and overall welding quality
Finest Practices for WPS Application
To make certain effective WPS execution in welding operations, adherence to market requirements and thorough focus to information are extremely important. When initiating WPS implementation, it is crucial to begin by thoroughly comprehending the details welding demands of the project. This involves a detailed testimonial of the welding treatment requirements, products to be bonded, and the environmental problems in which the welding will certainly take location.
Once the demands are clear, the next action is to select the ideal welding treatment that lines up with these requirements. This includes seeking advice from the pertinent codes and requirements, such as those given by the American Welding Culture (AWS) or the International Company for Standardization (ISO), to ensure compliance and quality.
Additionally, recording the entire WPS application procedure is important for traceability and quality control. Detailed documents need to be kept pertaining to welding parameters, product preparation, interpass and preheat temperature levels, welding consumables used, and any inconsistencies from the original procedure. Regular audits and reviews of the WPS can help recognize locations for improvement and make certain continuous optimization of the welding process.
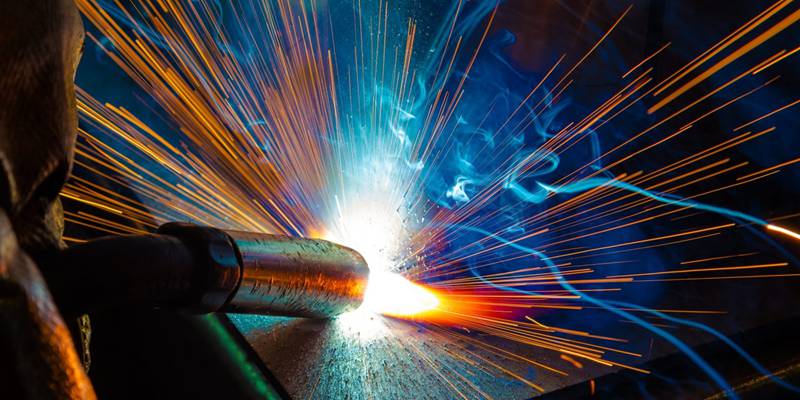

Final Thought
To conclude, the implementation and optimization of Welding Procedure Specifications (WPS) is vital for accomplishing welding excellence. By understanding the crucial elements of WPS, executing reliable approaches for optimization, addressing common difficulties, and complying with best techniques, welders can make certain top notch welds and visit this website safe working conditions. It is critical for professionals in the welding market to focus on the appropriate application of WPS to improve overall welding efficiency and attain desired results.
The Importance of Welding Treatment Requirements (WPS) in the welding market can not be overemphasized, serving as the foundation for guaranteeing consistency, high quality, and security in welding procedures. A WPS offers comprehensive directions on how welding is to be brought out, consisting of important variables such as materials, welding procedures, joint layout, filler More about the author steels, preheat and interpass temperatures, welding currents, voltages, traveling rates, and extra. One crucial element of a WPS is the welding process spec, which lays out the details welding processes to be used, such as gas tungsten arc welding (GTAW) or shielded metal arc welding (SMAW) By integrating these essential components right into the WPS, welding treatments can be standard, making certain quality, efficiency, and security in welding operations.
It is essential for specialists in the welding industry to prioritize the proper implementation of WPS to enhance overall welding efficiency and attain wanted end results.